Back
Thermo-Mechanical Analysis of Damaged Trailing Edge of Gas-Turbine Vane
การวิเคราะห์เชิงกลทางความร้อนของใบพัดกังหันแก๊สที่มีความเสียหายที่ขอบท้าย
@วิทยาลัยอุตสาหกรรมการบินนานาชาติ
#KLLC 2024
#Industry 4.0
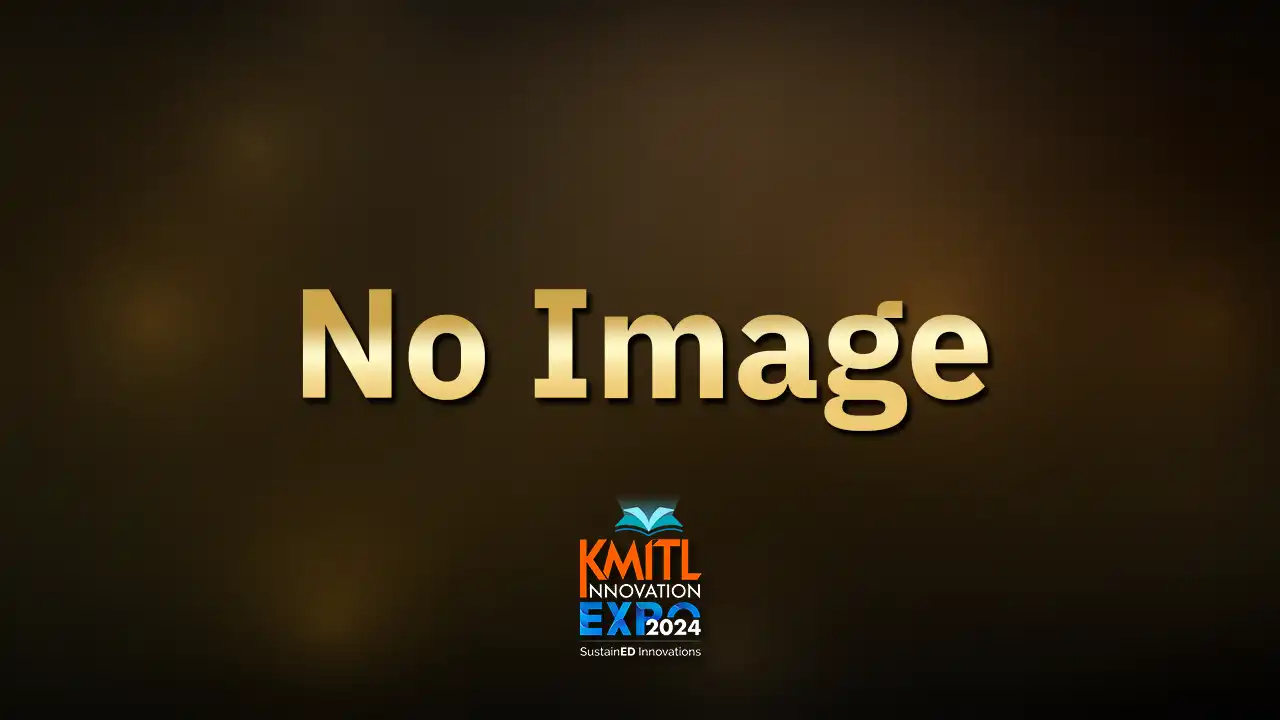
Details
A three-dimensional CFD simulation with the SST k-w turbulence model and conjugate heat transfer (CHT) analysis are used in this work for the upstream calculation to investigate flow and heat transfer phenomena at the vane trailing edge while subjected to damage effects. Then, for the downstream calculation, thermo-mechanical analysis is used to examine thermal stress variations. The profile of the Mark II vane is used to define vane boundaries in the computational domain. Broken scenarios in both the streamwise and spanwise directions are presented in a very simplified manner, with a short, shallow cutback expanding into a long, deep one, namely 0.1 cm x 1 cm to 0.3 cm x 3 cm. Flow phenomena such as streamlines, pressure, Mach number, and turbulent kinetic energy are presented as results. Furthermore, surface and body temperatures, as well as thermal stress, are discussed in order to demonstrate the effects of the damaged TE on thermo-mechanic phenomena. According to the findings, vane TE damage has a significant impact on fluid in motion and heat transfer phenomena.
Objective
Based on the Brayton cycle, an increment of the turbine inlet temperature (TIT) is a key to providing high efficiency for gas-turbine engines that are typically used for aircraft propulsion. Unfortunately, at high TITs, the turbine, particularly the nozzle guide vane (NGV), must operate in hostile environments with hot gas on a regular basis. As a result, the NGV material is susceptible to thermal fatigue failure during service. In modern gas-turbine engines, techniques of internal and external cooling have been developed to extend the lifespan of the NGV material and the survivability of NGVs has been investigated using aero-thermo-mechanic analysis. However, the improvement of the NGV's cooling effectiveness and efficiency remains challenging due to the complex phenomena of local heat transfer caused by convection and conduction, which must be balanced and compromised by coolant-hot gas management and design of vane configuration. The deterioration of the vane trailing edge (TE) is one example of this difficulty because the cooling of the vane TE is limited by its shape, flow physics and interaction around the TE region. Moreover, the vane may sustain damage such as a crack to its TE during operation. Certainly, this can have a negative effect on gas-turbine performance. There have been many numerical and experimental studies on flow physics and interaction between coolant and hot gas around the TE region, only a few studies have reported the effects of the damaged TE on flow behavior and gas-turbine heat transfer during operation. Therefore, a better understanding of the flow physics around the damaged TE, heat transfer, and corresponding thermal stress at the damaged TE is required.
Project Members
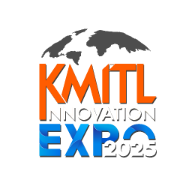
ชุติพันธ์ เชี่ยวสุวรรณ
CHUTIPHAN CHEOSUWAN
#นักศึกษา
Member
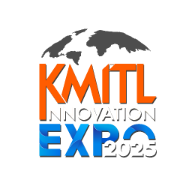
กสิณ กสิณธร
KASIN KASINTORN
#นักศึกษา
Member
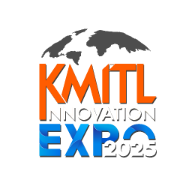
ประเสริฐ ประภามณฑล
Prasert Prapamonthon
#อาจารย์
Advisor
Vote for this Innovation!
Loading...
Powered By KMITL Innovation Project